Benders
Benders, also known as tube or pipe benders, are machines specifically designed to bend metal tubes or pipes into various shapes and angles. They are widely used in industries such as construction, plumbing, automotive, aerospace, and manufacturing. Benders typically consist of a sturdy frame or base with various components to facilitate the bending process. The key components of a typical tube or pipe bender include: [Bending Die:] The bending die is a curved or contoured component that determines the shape and angle of the bend. It is attached to the bender and holds the tube or pipe in place during the bending process. Bending dies come in different sizes and shapes to accommodate various tube diameters and bending requirements. [Mandrel:] In some benders, a mandrel is used to prevent the tube or pipe from collapsing or wrinkling during the bending process. The mandrel is inserted into the tube or pipe to provide internal support, ensuring a smooth and uniform bend.[Bender Controls:] Modern benders often have electronic or hydraulic controls to precisely control the bending process. These controls allow operators to set parameters such as bend angle, bend radius, and bend speed, ensuring accurate and repeatable results.
The bending process typically involves the following steps: [Tube or Pipe Preparation:] The tube or pipe to be bent is prepared by removing any burrs, ensuring the ends are cut squarely, and sometimes lubricating the surface to reduce friction.
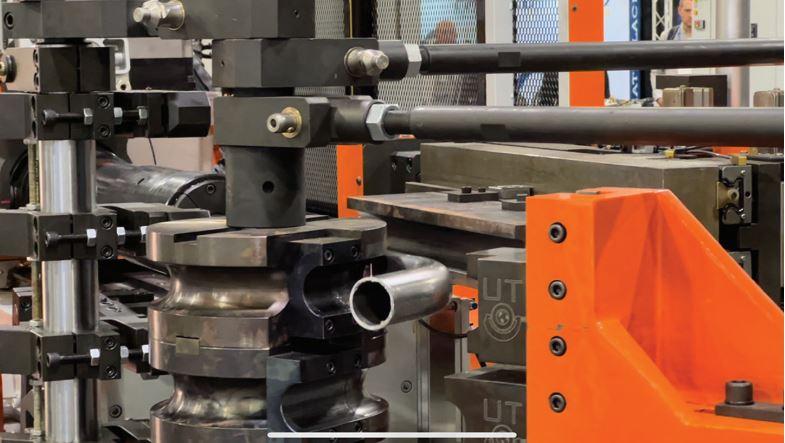
Benefits of Benders:
Benders, or tube/pipe benders, offer several benefits in various industries and applications. Here are some advantages of using benders:
Precise Bending
Benders enable precise bending of metal tubes or pipes. They allow for accurate control over the bending angle, radius, and shape, ensuring consistency and precision in the formed components. This is crucial for applications where precise dimensions and fit are required, such as plumbing systems or structural frameworks.
Customization and Flexibility
Benders offer flexibility in creating custom bends and shapes according to specific project requirements. They can produce bends in different angles, curves, or multiple planes, allowing for the creation of complex geometries. This customization capability makes benders valuable for applications that demand unique or specialized bending configurations.
Reduced Material Waste
Benders minimize material waste by accurately shaping tubes or pipes without excess material. They can bend the material to the desired angle or shape while maintaining the integrity of the remaining portion. This leads to optimized material usage, cost savings, and reduced environmental impact.
Improved Structural Integrity
Benders can create bends in metal tubes or pipes without compromising their structural integrity. By utilizing appropriate bending techniques and avoiding excessive deformation, benders can maintain the strength and integrity of the material. This is crucial for applications where the structural integrity of the bent component is critical, such as in pipelines or load-bearing structures.
Ease of Use and Setup
Benders are designed to be user-friendly and easy to set up. They often come with adjustable settings and intuitive controls, making them accessible to operators with varying levels of experience. Quick setup and changeover times allow for efficient workflow and flexibility in bending operations.
Versatility
Benders are highly versatile machines that can bend a wide range of materials, including steel, aluminum, copper, and stainless steel. They can accommodate different tube or pipe sizes and thicknesses, making them suitable for various applications across multiple industries.
Time and Cost Savings
Benders can save time and costs in metal fabrication processes. They offer faster and more efficient bending operations compared to manual methods, reducing production time and increasing productivity. By automating the bending process, benders eliminate the need for manual labor, reducing labor costs and minimizing the risk of errors.
Consistency and Repeatability
Benders ensure consistent and repeatable results across multiple bends. With proper tooling setups and adjustments, benders provide uniformity in the bending process, ensuring consistent quality and fit in the produced components. This consistency is essential for assembly, interchangeability, and overall product integrity.
Safety Features
Modern benders are equipped with safety features to protect operators during the bending process. These features include safety guards, emergency stops, and interlocks. They ensure safe operation, prevent accidents, and comply with safety regulations.